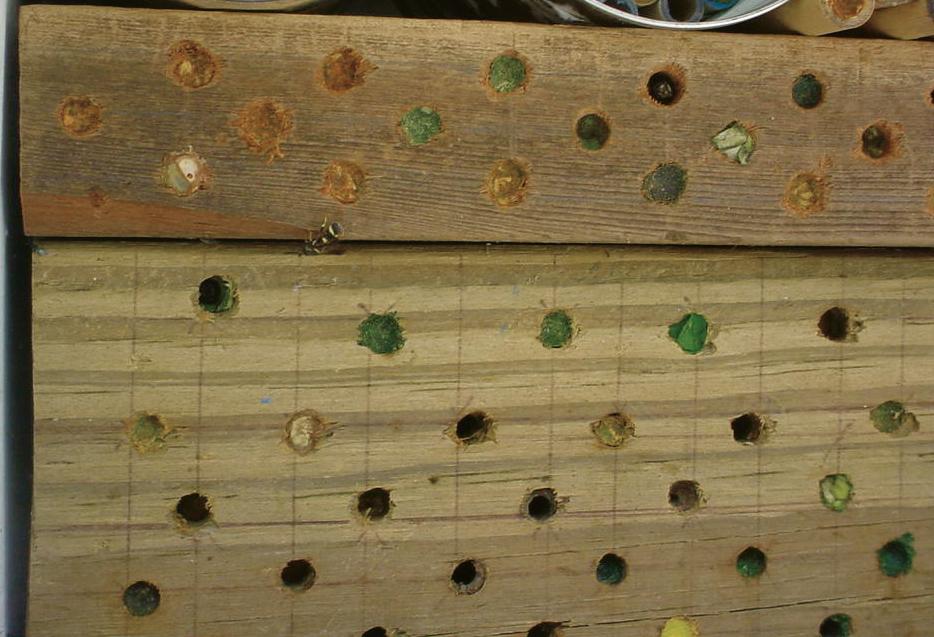
Historically leafcutter bee nests consisted of drilled pine or fir boards, usually 3 to 4 inches by 4 to 6 inches (~7.6 to 10 centimeters by 10 to 15 centimeters) in width, and often up to 4 feet (~1.2 meters) in length. Boards were drilled with a series of dead-end holes for nest tunnels. Such nests were extremely attractive to bees and convenient because the bees could be stored and incubated within the boards (Figure 7.13).
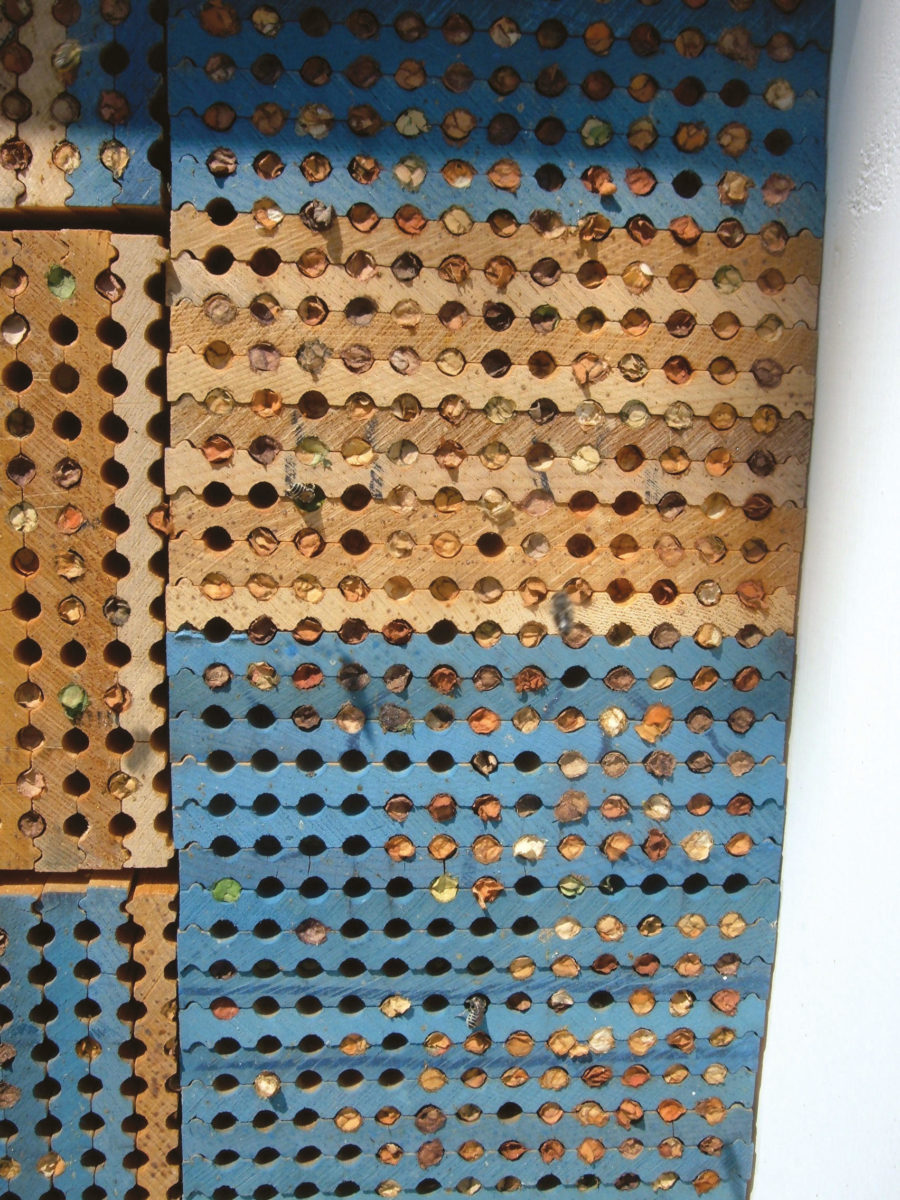
However, because the inner nest surfaces could not be exposed for cleaning, and because the boards were continually filled with bee larvae, these nests became contaminated with a fungal disease called chalkbrood (Ascosphaera aggregata). By the 1980s US beekeepers who continued to manage bees in solid boards saw significant annual losses. To reduce the spread of chalkbrood spores, beekeepers began phasing out solid boards on an annual basis, drilling out the tunnels to remove dead bees and leaf debris. This labor-intensive practice resulted in the term re-drill in reference to solid wood nest boards.
While re-drills were the standard American nest for many years, Canadian leafcutter producers pioneered new nest designs that facilitated the annual removal of cells from the nest. Among these nest designs were solid wood blocks that were drilled completely through, and grooved boards (often called laminates) that consisted of a series of channels routed into the boards, which were stacked together to form a series of tunnels (Figure 7.14). These nest types were originally constructed of wood; however, today they are only commonly available as Styrofoam with fabric or foam backing material which is held in place by a series of sheet metal clamps or elastic straps (Figure 7.15).
These loose-cell nests have a tremendous advantage because they can be completely disassembled and cleaned each season. In addition, the loose cells require significantly less space for cold storage and incubation than solid boards filled with bees. There are several disadvantages with loose-cell nests, including the potential for greater parasite problems due to the less secure backing material and the poor durability of Styrofoam nests.
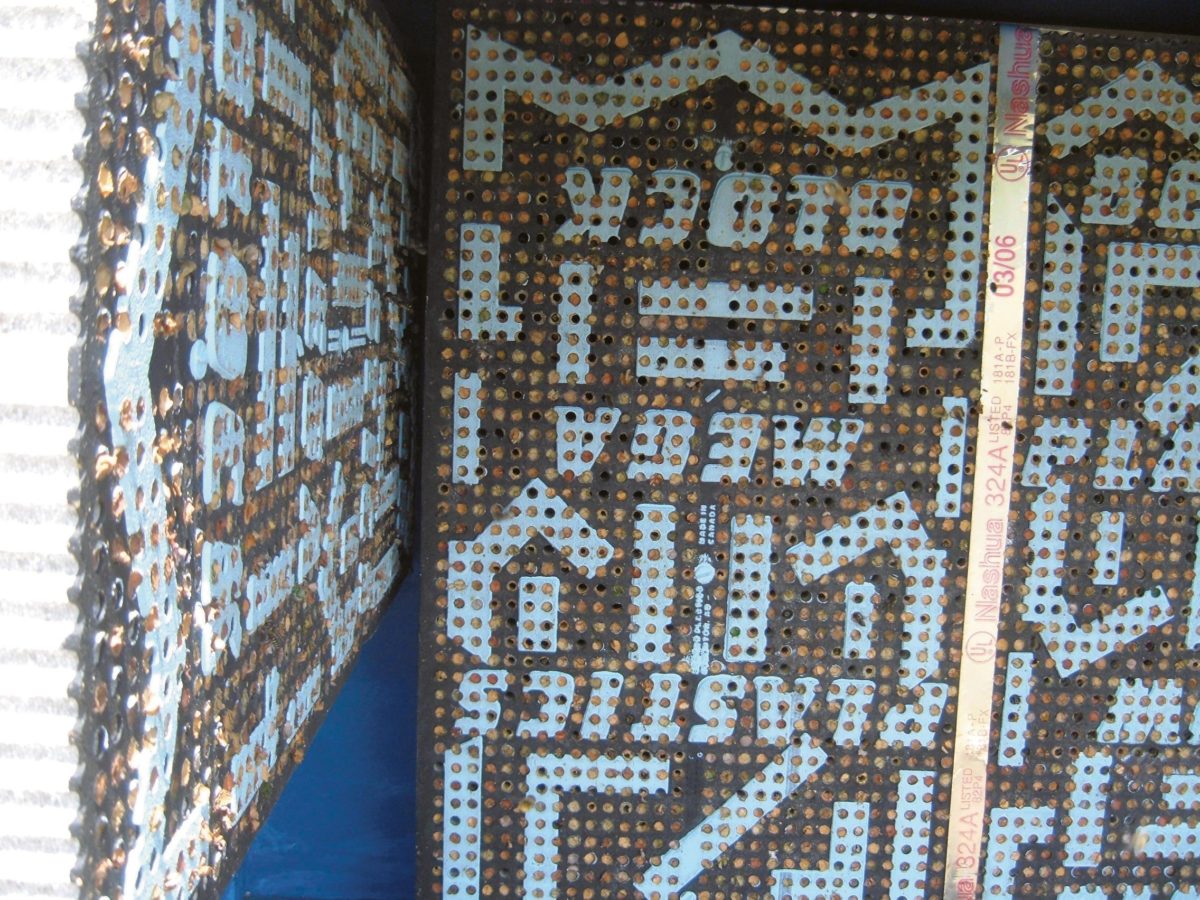
Various other nest materials have been used for leafcutter bees, including paper straws and fluted cardboard consisting of a series of tunnel corrugations affixed to a single sheet of paper backing, which is then coiled onto itself forming a round spiral of tunnels. Like the loose-cell nests described above, these paper and cardboard nest materials are much more prone to infestation by parasites than solid wood blocks.
A significant amount of research has been performed on the nesting preferences of leafcutter bees. Tunnel diameter, depth, material, color, and hole density have all been explored, and in many cases the results have been contradictory or inconclusive. General guidelines are as follows: tunnels should be between 15/64 and 1⁄4 inch in diameter (6 to 6.4 millimeters), and 3 inches to 6 inches in depth (7.6 to 15 centimeters). Nest surfaces should be dark in color, with anecdotal evidence suggesting that blue and black colors are most attractive.
Nest dimensions should be configured to promote bee health and maximize female production, as well as facilitate ease of orientation for foragers returning to the nest. Larger (1⁄4 inch, 6.4 millimeters) and deeper (4 to 6 inches, 100 to 150 millimeters) holes should be used when possible as they encourage larger, healthier brood as well as a higher proportion of female offspring. Inter-hole distances of 3⁄8 inch (9.5 millimeters), or even higher, will result in easier orientation for female bees that are returning to the nest from foraging trips. Bees that can easily find their nest hole will complete nests more quickly, and are less likely to enter the wrong nest holes where they could become contaminated with disease spores. Commercially available Styrofoam nests tend to have very high hole densities. Similarly, nests with painted, raised or textured orientation patterns, and irregular surfaces (such as wood), all result in easier orientation for returning foragers.
Currently no single nest type is free of problems, and there is much room for experimentation. It is likely that an optimal nest for small producers may be a hybrid of some of the systems listed above— a solid block with removable inserts for example (see Appendix E). Such a system would no doubt greatly increase labor, but would probably result in a higher percentage of healthy female bees. For more information on the benefits and drawbacks of loose-cell verses solid-board nests, see Appendix F.